Providing Better Solutions For Families
Digital Experience

Online Safety Expert
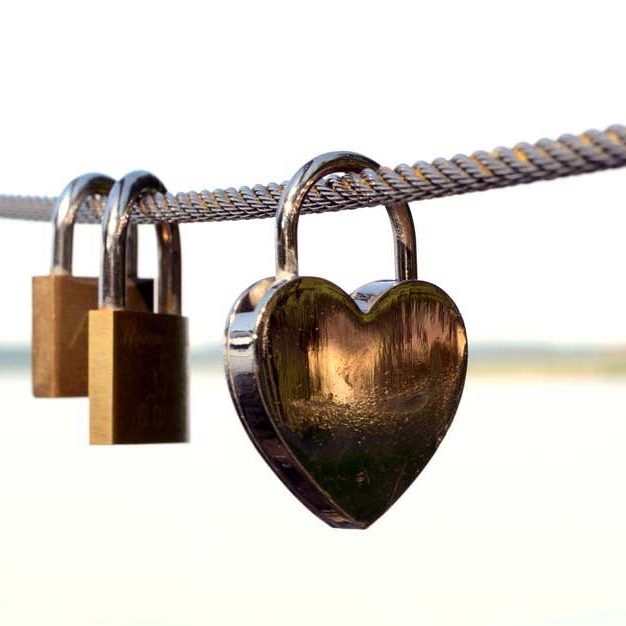
Working For Future
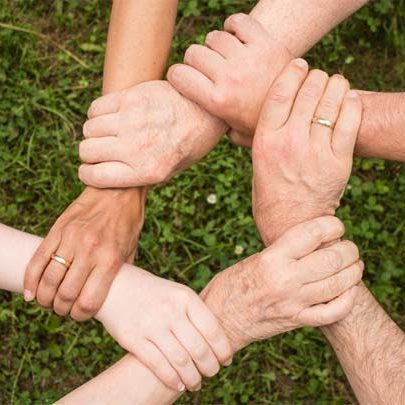
WORKSHOPS AND SPEAKING
SGCVIP is a dynamic and engaging online platform that has quickly risen to prominence due to its exceptional features and surprises. The site captivates users with its creative content and interactive tools providing a refreshing experience that stands out in the digital landscape. What sets we apart is its ability to offer users unexpected delights keeping them coming back for more. The platform has seen a remarkable surge in attention as a result of its commitment to delivering quality content that resonates with a diverse range of interests. With a focus on user satisfaction SGCVIP has created an environment that fosters excitement and anticipation. Its popularity continues to grow as more users discover the platforms captivating surprises. SGCVIP is shaping the future of digital engagement with its fresh approach and exciting content.
Helping Families Have a Positive and Safe Experience Online
LATEST NEWS...
What Makes a Great Photovoltaics Supplier in the European Market?
December 4, 2024
In the competitive landscape of the European photovoltaics market, identifying the hallmarks of a great supplier is essential for stakeholders seeking reliable partnerships. Key factors such as product quality, innovation, and robust customer support play critical roles, yet they merely scratch the surface. As the market increasingly emphasizes compliance with stringent regulations and ethical sourcing, understanding how these elements interconnect can provide valuable insights. What other attributes might elevate a supplier in this dynamic environment? Exploring these considerations reveals more than just operational excellence; it uncovers the strategic advantages that define market leaders.
Quality of Products
Quality is a critical determinant in the competitiveness of photovoltaics suppliers within the European market. The selection of a supplier often hinges on the reliability and efficiency of their products, as these factors directly influence energy output and long-term performance. Data indicates that high-quality photovoltaics can enhance energy yields by up to 20% compared to lower-grade alternatives, underscoring the importance of product excellence. In addition, certifications such as IEC 61215 and IEC 61730 serve as benchmarks for evaluating quality standards, helping stakeholders identify the best photovoltaics supplier. As the market evolves, suppliers committed to rigorous quality control and testing mechanisms will not only gain consumer trust but also secure a competitive edge in this rapidly growing sector. Click over here to discover wholesale photovoltaics.
Commitment to Innovation
A strong commitment to innovation is paramount for photovoltaics suppliers aiming to thrive in the competitive European market. As the renewable energy landscape evolves, suppliers must adopt cutting-edge technologies to enhance efficiency and reduce costs. For instance, advancements in solar panel materials, such as bifacial and perovskite solar cells, can greatly improve energy output. Moreover, a focus on smart grid integration and energy storage solutions is essential for suppliers to meet the growing demand for reliable energy sources. In the wholesale photovoltaics sector, suppliers that prioritize research and development are better positioned to offer superior products and attract discerning customers. Ultimately, innovation not only enhances product quality but also fosters sustainable growth within the European photovoltaics market.
Customer Service Excellence
Delivering customer service excellence is critical for photovoltaics suppliers in the European market, where consumer expectations are increasingly shaped by both service quality and product performance. Research indicates that over 70% of customers prioritize responsive support in their purchasing decisions, particularly concerning solar panel installations. Suppliers that invest in robust customer service frameworks—such as extensive after-sales support, timely communication, and effective problem resolution—tend to foster stronger customer loyalty. An analysis of market leaders reveals that those with high customer satisfaction ratings often achieve a 20-30% increase in repeat business, underscoring the importance of service excellence. In an industry characterized by rapid technological advancements, prioritizing customer service is not just beneficial; it is essential for maintaining a competitive edge.
Compliance With Regulations
Maneuvering the complex landscape of compliance with regulations is paramount for photovoltaics suppliers operating in the European market. The European Union (EU) has established stringent regulations aimed at promoting solar power while ensuring environmental sustainability and consumer protection. Suppliers must adhere to directives such as the Renewable Energy Directive and the Ecodesign Directive, which set standards for product efficiency and lifecycle management. Non-compliance can result in significant penalties and loss of market access. In addition, the EU’s ongoing commitment to the Green Deal necessitates that suppliers remain agile, adapting to evolving policies. Regular audits and certifications are critical to maintaining compliance and fostering trust with stakeholders, positioning suppliers as reliable partners in the burgeoning solar power sector.
Ethical Sourcing Practices
Increasingly, photovoltaics suppliers in the European market are recognizing the importance of ethical sourcing practices as a core component of their business strategy. In the Czech Republic, for instance, the push for sustainable solar energy has driven companies to adopt transparent supply chains that prioritize environmental responsibility and fair labor practices. Research indicates that consumers are more likely to support brands that demonstrate commitment to ethical sourcing, which can enhance brand loyalty and market share. By integrating ethical standards, suppliers not only comply with stringent European regulations but also contribute to the broader goal of sustainable development. This trend is reshaping the competitive landscape, where ethical sourcing is becoming a pivotal factor in supplier selection and overall market success.
Conclusion
In conclusion, the characteristics defining a great photovoltaics supplier in the European market encompass a robust commitment to product quality, innovation, and customer service. Adherence to stringent regulations and ethical sourcing practices further enhances brand reputation and market access. The interplay of these factors not only guarantees operational efficiency and reliability but also fosters customer loyalty and competitive advantage. Consequently, suppliers that prioritize these elements are better positioned to thrive in the evolving energy landscape.
When Is the Right Time to Hire a Digital Marketing Agency in Prague?
December 3, 2024
If you’ve noticed that your marketing efforts are stalling, it might be time to reflect on hiring a digital marketing agency in Prague. When engagement metrics plateau or your in-house team struggles with the latest strategies, outsourcing can bring fresh perspectives and expertise. Limited time can also hinder your marketing effectiveness, making professional support a viable solution. But how do you know when these signs become critical? Exploring the specific indicators can clarify your next steps and potentially transform your approach to digital marketing.
Signs Your Marketing Efforts Are Stagnant
Have you noticed your engagement metrics plateauing despite your best efforts? It’s frustrating when you pour time and resources into your marketing strategies, only to see minimal results. If your social media interactions, website traffic, or conversion rates have stalled, it might be time to reassess your approach.
Consider how often you’re experimenting with new content formats or channels. If you’re sticking to the same routine, your audience may have grown tired of your messaging. Regularly rejuvenating your strategies is key to keeping your brand relevant and engaging.
Another sign of stagnation is audience feedback. If your followers aren’t responding, or worse, if you’re receiving negative comments, it’s a clear indicator that your content isn’t resonating.
Lastly, take a look at your competitors. If they’re consistently innovating and capturing your audience’s attention, you may be falling behind in the digital landscape.
Partnering with a digital agency in Prague can provide fresh insights and expertise. They can help you revitalize your marketing efforts and boost your engagement metrics. Don’t let stagnation hold you back—embrace change and reach out for professional support when needed.
Lack of Expertise in Your Team
If your team lacks the necessary expertise in digital marketing, you’re likely missing out on valuable opportunities to connect with your audience and drive growth. In today’s fast-paced digital landscape, specialized knowledge is essential. Without it, you may struggle with vital strategies like SEO, content marketing, or social media engagement.
Hiring a marketing agency in Prague can bridge this gap effectively. These agencies are staffed with professionals who bring a wealth of experience and knowledge to the table. They understand the latest trends, tools, and techniques that can elevate your brand’s online presence. By leveraging their expertise, you can develop targeted campaigns that resonate with your audience, ensuring you make the most of your marketing budget.
Moreover, a marketing agency in Prague can provide you with fresh perspectives and innovative ideas that your in-house team might overlook. This collaboration not only fills the skills gap but also allows your team to focus on core functions while experts handle your digital marketing strategy. Ultimately, investing in the right agency can transform your approach, yielding measurable results and sustainable growth for your business. Don’t let a lack of expertise hold you back; consider bringing in the professionals.
Limited Time for Marketing Activities
How can you effectively manage your marketing activities when time is a scarce resource? In today’s fast-paced business environment, juggling multiple responsibilities can leave you with little time for marketing. This is where hiring a digital agency can make all the difference. By outsourcing your marketing efforts, you free up valuable hours to focus on your core business functions.
A digital agency specializes in strategic planning, content creation, and campaign management. They have the expertise and tools to streamline your marketing processes, ensuring that your brand stands out without draining your time. Instead of struggling to keep up with trends and algorithms, you can rely on their knowledge to implement effective strategies that drive results.
Moreover, a digital agency can quickly adapt to market changes, managing campaigns efficiently so you can stay relevant. Think of this as an investment in your business’s growth. By delegating your marketing tasks, you can concentrate on what you do best while experts handle the complexities of digital marketing. In the end, partnering with a digital agency could be the key to releasing your business’s full potential while conserving your most precious resource—time.
Need for Advanced Strategies and Tools
In the competitive landscape of digital marketing, the necessity for advanced strategies and tools is undeniable. You’re not just competing for attention; you’re vying for the loyalty of an audience that’s bombarded with choices. To stand out, you need to leverage sophisticated techniques like data analytics, automation, and targeted content marketing.
Hiring a digital marketing agency in Prague can provide you with the expertise and resources you might lack in-house. These agencies are equipped with cutting-edge tools that can analyze market trends, optimize your campaigns, and improve your ROI. They can help you navigate the complexities of SEO, PPC, social media, and email marketing—ensuring that every aspect of your digital marketing strategy is working in harmony.
Moreover, as algorithms evolve, keeping up with the latest trends and tools can be overwhelming. An agency’s dedicated team can stay on top of these changes, allowing you to focus on your core business. Investing in advanced strategies not only enhances your brand’s visibility but also fosters long-term growth. If you’re serious about elevating your digital marketing efforts, it’s time to contemplate enlisting professional help.
Conclusion
So, if you’re feeling like your marketing is stuck in neutral, it might be time to contemplate a digital marketing agency. After all, why not let experts handle the heavy lifting while you focus on what you do best—like deciding what’s for lunch? Embracing fresh strategies and insights can breathe new life into your brand, proving that sometimes, the best way to move forward is to hand over the reins. Who knew outsourcing could be your secret weapon?
How to Choose the Right China Press Brake Machine for Your Business?
November 30, 2024
Selecting the appropriate China press brake machine for your business is a critical decision that requires careful consideration of various factors. Key elements such as production needs, machine specifications, and tonnage requirements must align with your operational goals to guarantee efficiency and precision. Additionally, evaluating control systems and financial implications can considerably impact your long-term success. As you navigate these complexities, understanding how each component interacts could mean the difference between a successful investment and unforeseen challenges. What considerations will ultimately guide your choice?
Assess Your Production Needs
When determining the most suitable China press brake machine for your operations, it is crucial to assess your production needs meticulously. Begin by evaluating the types of materials you will be working with, as different metals and thicknesses require specific bending capabilities. Consider the volume of production; high-volume operations may necessitate a more robust machine, while smaller projects could be managed with a less powerful model. Additionally, analyze the complexity of the bending tasks; intricate designs demand advanced features. Research available options, such as the Shenchong press brake for sale, to find a model that aligns with your requirements. By thoroughly understanding your production needs, you can guarantee your investment in a press brake machine supports efficient and effective operations.
Understand Machine Specifications
Understanding the specifications of a China press brake machine is essential for making an informed purchasing decision. Key specifications include bending capacity, which defines the maximum material thickness and width the machine can accommodate. Additionally, consider the machine’s overall dimensions, stroke length, and open height, as these factors affect the type of projects you can undertake. The control system—whether manual, CNC, or hybrid—also greatly impacts precision and ease of operation. Moreover, pay attention to the materials used in construction, as they contribute to the machine’s durability and maintenance requirements. When evaluating options, verify you are sourcing from reliable suppliers who offer a range of China press brake machine for sale, allowing for comparisons based on specifications that meet your business needs.
Evaluate Tonnage Requirements
Evaluating tonnage requirements is a critical step in selecting the appropriate China press brake machine for your operations. Tonnage refers to the amount of force needed to bend a specific material thickness and type. To accurately determine your needs, consider the material’s tensile strength, thickness, and the desired bend angle. A general rule of thumb is that a press brake requires approximately 1 ton of pressure per 1 inch of material width for standard steel. However, variations exist based on material properties and bend geometry. Selecting a press brake with insufficient tonnage can result in inadequate performance, while excessive tonnage may lead to increased operational costs. As a result, precise calculations are essential to guarantee ideal machine selection and efficiency.
Choose the Right Control System
Selecting the appropriate control system for your China press brake machine is essential for optimizing performance and ensuring accuracy in bending operations. The control system dictates the machine’s responsiveness and operational precision, directly impacting production efficiency. Two primary types of control systems are available: manual and CNC (Computer Numerical Control). Manual systems offer simplicity and lower initial costs, suitable for basic applications. In contrast, CNC systems provide advanced programming capabilities, facilitating complex bends and enhanced repeatability, making them ideal for high-volume production environments. Additionally, consider user interface design, ease of programming, and compatibility with existing systems. An informed choice in the control system will not only elevate operational capabilities but also contribute to long-term productivity and cost-effectiveness in your press brake operations.
Consider Budget and Financing Options
Budget considerations play a pivotal role in the acquisition of a China press brake machine, influencing both the initial purchase and long-term operational costs. When evaluating high quality press brakes, it is essential to analyze not only the purchase price but also the expenses related to maintenance, energy consumption, and potential downtime. Financing options such as leasing or loans can also impact budget flexibility, allowing businesses to acquire advanced machinery without immediate full payment. It is advisable to assess total cost of ownership, including warranties and service contracts, to guarantee that the chosen financing aligns with the company’s financial strategy. Ultimately, a thorough budget assessment will aid in selecting a press brake that meets operational needs while remaining financially viable.
Conclusion
Selecting the appropriate China press brake machine necessitates a thorough evaluation of production requirements, machine specifications, tonnage needs, and control systems. A complete understanding of these factors guarantees optimized bending processes and operational efficiency. Additionally, careful consideration of budgetary constraints and financing options is essential for achieving a sustainable investment. By systematically analyzing these components, businesses can enhance productivity and guarantee the long-term success of their manufacturing operations.
Why a Strong Password Generator Is Essential for Safe Online Accounts?
November 18, 2024
In an increasingly digital world, the security of online accounts hinges markedly on the strength of passwords utilized. A strong password generator is not merely a convenience but a critical tool that creates complex, unique passwords, thereby mitigating the risk of unauthorized access. By employing sophisticated algorithms, these generators craft unpredictable passwords that thwart cybercriminals’ attempts at breaching accounts.
However, understanding the intricacies of password vulnerabilities and the benefits of utilizing such generators is essential to fully grasp their impact on online security. What factors should one consider in choosing the most effective password generator?
Understanding Password Vulnerabilities
In the domain of online security, understanding password vulnerabilities is essential for safeguarding personal and sensitive information. Weak passwords remain a primary target for cybercriminals, who utilize sophisticated methods such as brute force attacks and dictionary attacks to compromise accounts. A strong password, characterized by its complexity and unpredictability, greatly mitigates these risks.
Utilizing a password generator strong enough to create unique combinations of letters, numbers, and symbols can enhance password strength, making it difficult for unauthorized users to gain access. In addition, awareness of common vulnerabilities, such as password reuse and simplistic patterns, is vital in developing effective security protocols. By prioritizing strong password creation and employing advanced tools, individuals can effectively bolster their online defenses against persistent cyber threats.
Benefits of Unique Passwords
Creating unique passwords for each online account greatly enhances security by reducing the risk of unauthorized access. When a password is reused across multiple accounts, a breach in one can compromise all others, exposing sensitive information. Unique passwords minimize this risk by containing distinct combinations of characters that are difficult to guess or crack. Additionally, they can thwart automated attacks, such as credential stuffing, where attackers use stolen credentials from one site to gain access to others.
Unique passwords also promote better security hygiene, encouraging users to take password management seriously. This practice not only protects individual accounts but also contributes to overall cybersecurity, making it more challenging for cybercriminals to exploit vulnerabilities across various platforms.
How Password Generators Work
Password generators utilize algorithms that create complex combinations of characters to produce secure passwords. These algorithms often incorporate various elements, such as uppercase and lowercase letters, numbers, and special symbols, guaranteeing a diverse range of potential characters. By employing randomization techniques, password generators can considerably enhance the unpredictability of the generated passwords, making them resistant to brute-force attacks.
Some advanced generators also allow users to specify criteria, such as minimum length or required character types, tailoring the output to specific security needs. In addition, many password generators utilize entropy-based methods, evaluating the unpredictability of generated passwords against established standards. This mathematical approach guarantees that the passwords not only meet complexity requirements but also provide a robust defense against unauthorized access.
Choosing the Right Password Generator
How can one effectively choose the right password generator to guarantee ideal security for online accounts? First, assess the generator’s security features, such as encryption and the use of secure algorithms. A reputable generator should incorporate randomness and complexity to prevent predictability. In addition, look for customizable options that allow users to define password length and character types, enhancing security according to individual needs.
User reviews and expert recommendations can provide insights into the effectiveness and reliability of various tools. Moreover, consider whether the generator integrates with password managers, facilitating seamless password storage and usage. Ultimately, selecting a password generator that balances security features with user-friendliness is vital for maintaining robust online account protection.
Maintaining Online Security Practices
Effective management of online security practices is essential in safeguarding personal information and digital assets. Regularly updating passwords and employing unique passwords for different accounts reduces the risk of credential theft. Users should also enable two-factor authentication (2FA) where available, adding an extra layer of protection against unauthorized access. Moreover, being vigilant about phishing attempts and suspicious links is vital; these tactics are often used to compromise accounts.
Regularly reviewing account activity can help identify unauthorized access early. Additionally, utilizing a reputable password manager facilitates the secure storage and generation of complex passwords. Ultimately, a proactive approach to online security practices not only protects individual accounts but also contributes to broader cybersecurity resilience.
Conclusion
To summarize, the implementation of a strong password generator is essential for safeguarding online accounts against unauthorized access. By generating complex, unique passwords, these tools mitigate the risks associated with password vulnerabilities, enhance overall cybersecurity, and promote effective password management. Selecting an appropriate password generator and adhering to best online security practices further reinforces protection. Ultimately, the use of strong password generators serves as a fundamental strategy in the ongoing effort to protect sensitive information in the digital landscape.
Tips for Selecting the Best Sports Nutritional Supplements
November 18, 2024
Selecting the ideal sports nutritional supplements requires a strategic approach, as the market is flooded with options that claim to enhance performance and recovery. It is essential to begin by clarifying your specific athletic goals, which will inform the types of supplements most beneficial to you. Further, understanding product ingredients and their credibility can considerably affect both safety and effectiveness. However, maneuvering these factors can be complex; exploring the nuances of each step can lead to informed choices that align with your unique needs. What important considerations should you keep in mind as you make this selection?
Understand Your Goals
To effectively select sports nutritional supplements, it is essential to first clarify your specific goals. Understanding whether your primary aim is to enhance performance, promote recovery, or support overall health will guide your nutrition choices. For instance, athletes focused on muscle gain may benefit from protein-rich supplements that provide essential nutrients for muscle synthesis. Conversely, endurance athletes might prioritize supplements that offer carbohydrates and electrolytes to maintain energy levels. Additionally, it’s vital to take into account the timing of supplement intake, as this can greatly influence nutrient absorption and effectiveness.
When choosing supplements, consider ingredients like AstraGin. This natural compound, derived from Astragalus and Panax Notoginseng, is known to enhance nutrient absorption, particularly for amino acids, vitamins, and minerals. Including AstraGin in your supplement regimen can improve the bioavailability of key nutrients, ensuring your body receives optimal support for your performance and recovery goals. By setting clear objectives and considering absorption enhancers like AstraGin, you can streamline your supplement selection process, ensuring that the products you choose align with your unique nutritional needs and performance aspirations.
Research Product Ingredients
When selecting sports nutritional supplements, thorough research of product ingredients is essential to confirm safety, efficacy, and compatibility with your individual health needs. Key ingredients such as prohydrolase, an enzyme that enhances protein digestion, can greatly impact your body’s ability to utilize nourishment effectively. Understanding the role of various components—such as amino acids, vitamins, and minerals—can help you make informed choices that align with your fitness objectives. Additionally, examining the source of ingredients guarantees they are derived from reputable suppliers, minimizing the risk of contamination or harmful additives. Prioritize transparency in labeling and seek products that provide detailed information on ingredient sourcing and functionality, empowering you to optimize your nutritional strategy for improved performance and recovery.
Check for Certifications
Verification of product certifications is a vital consideration in the selection of sports nutritional supplements. Certifications from reputable organizations, such as NSF International or Informed-Sport, indicate that a product has been tested for quality, safety, and compliance with label claims. For example, supplements containing ingredients like Carnosyn, a patented form of beta-alanine, should ideally have certification to guarantee they meet stringent purity standards. Additionally, products featuring Noolvl, known for enhancing cognitive function and exercise performance, should also be verified to confirm their efficacy and absence of harmful contaminants. By prioritizing certified products, consumers can make informed choices that enhance their athletic performance while minimizing health risks. Always check for these certifications before purchasing any supplement.
Read Customer Reviews
Reading customer reviews is an essential step in the process of selecting sports nutritional supplements, as these insights can reveal real-world experiences and outcomes associated with specific products. Reviews often highlight the effectiveness and potential side effects of supplements like instaminos, providing a balanced view of their impact on health. Consumers frequently share their testimonials regarding the improvements in performance, recovery times, and overall well-being. By examining these reviews, you can identify common themes and red flags, such as adverse reactions or unmet expectations. Additionally, consider the credibility of the reviewers, focusing on those who have similar fitness goals or dietary needs. Ultimately, informed decisions backed by genuine customer experiences can lead to better choices in sports nutritional supplementation.
Consult a Healthcare Professional
Consulting a healthcare professional is an essential step in the process of selecting sports nutritional supplements. Experts can provide personalized guidance based on individual health status, dietary needs, and fitness goals. They can help assess the efficacy of ingredients, such as astragin, which is known for enhancing nutrient absorption and bioavailability. A healthcare professional can also identify potential interactions with existing medications or conditions, ensuring safe supplementation. Additionally, they can recommend specific nutritional supplements that align with your athletic performance objectives. By seeking professional advice, athletes can make informed decisions that optimize their nutrition strategy while minimizing health risks. Ultimately, this approach fosters a balanced and effective supplementation routine tailored to individual requirements.
Conclusion
To sum up, selecting the best sports nutritional supplements necessitates a systematic approach. Defining specific goals, thoroughly researching product ingredients, verifying certifications, examining customer feedback, and seeking professional guidance are critical steps in ensuring safety and efficacy. This thorough evaluation not only enhances performance but also supports recovery, ultimately contributing to improved athletic outcomes. Adhering to these guidelines fosters informed decision-making, thereby maximizing the benefits derived from nutritional supplementation in sports endeavors.
What You Need to Know About Pest Control in Southern Norway?
November 17, 2024
If you’re living in Southern Norway, it’s important to understand the unique pest challenges you might face throughout the year. From the surge of ants in the warmer months to the mice looking for warmth in autumn, knowing these patterns can help you take the right precautions. You might think maintaining cleanliness is enough, but there’s more to effective pest control than meets the eye. What happens when you encounter a larger infestation or can’t identify a pest? The answers could change how you approach pest management in your home.
Common Pests in Southern Norway
In Southern Norway, residents often encounter a variety of common pests that can disrupt daily life. These pests include ants, cockroaches, mice, and wasps, each presenting unique challenges. Ants often invade homes in search of food, while cockroaches can spread diseases and trigger allergies. Mice not only contaminate food but can also cause structural damage. Wasps, particularly during late summer, can become aggressive and pose a sting risk.
Effective pest control is essential for managing these common pests in Southern Norway. Early detection is key; regular inspections can help you identify potential infestations before they escalate. You should seal entry points, reduce clutter, and maintain cleanliness to deter pests. If you encounter a significant infestation, consider professional pest control services. These experts employ targeted treatments that are safe and effective, tailored to the specific pest issue.
Seasonal Pest Challenges
Southern Norway’s changing seasons bring unique pest challenges that require vigilance and adaptive strategies. As winter fades, pests like ants and cockroaches emerge, seeking warmth and food. Spring is particularly active, with wasps and mosquitoes becoming more prevalent. These pests can disrupt outdoor activities and pose health risks.
During summer, the warm weather leads to a spike in pest populations. You might notice an increase in flies, beetles, and ticks, which can affect both your home and your pets. It’s vital to monitor these pests closely, as they can multiply rapidly in favorable conditions.
Effective Prevention Strategies
To keep pests at bay throughout the year, implementing effective prevention strategies is vital. Start by sealing cracks and crevices around your home, as these serve as entry points for pests like silverfish. Pay particular attention to areas around windows, doors, and foundations. Next, keep your home clean and clutter-free. Regularly vacuuming and dusting can eliminate potential habitats and food sources for silverfish and other pests.
Moisture control is imperative in prevention. Silverfish thrive in humid environments, so consider using dehumidifiers in basements and bathrooms. Fix any leaks promptly and guarantee proper ventilation throughout your home. Store food in airtight containers and promptly clean up spills to reduce food availability.
In addition, inspect your home for any signs of pests regularly. Early detection can help you tackle issues before they escalate. Finally, consider outdoor measures like trimming vegetation away from your home’s exterior and guaranteeing proper drainage. By following these strategies, you’ll create an environment that’s less inviting to silverfish and other pests, making your home a safer and more comfortable place.
Safe Pest Control Methods
After implementing preventive measures, it’s important to contemplate safe pest control methods for effective management. If you’ve spotted mice in your house, there are several approaches you can take that minimize risks to your family and pets.
Firstly, consider using traps. Snap traps are effective and can be placed in areas where you’ve noticed mouse activity. Always check traps regularly to guarantee swift removal of any caught mice. Alternatively, you can opt for humane traps that allow for relocation.
Secondly, natural repellents can be effective. Essential oils like peppermint or eucalyptus may deter mice. Soak cotton balls in these oils and place them in areas where mice are commonly found.
When to Call Professionals
While you may successfully manage minor pest issues on your own, there are instances when calling in professionals becomes necessary. If you notice signs of rats in your house, such as droppings, gnaw marks, or unusual noises, it’s time to act swiftly. Rodents can pose serious health risks and cause considerable damage to your property.
Another situation that warrants professional help is when the infestation is extensive. If you’ve tried over-the-counter traps or poisons without success, it’s essential to seek expert assistance. Professionals have the training and resources to identify the source of the problem and implement effective control measures.
Additionally, if you’re unsure about the type of pest you’re dealing with, don’t hesitate to call an expert. Misidentification can lead to ineffective treatments and prolonged issues. Pest control experts can accurately diagnose the problem and recommend appropriate solutions.
Conclusion
In Southern Norway, the contrast between thriving pest populations and your home’s well-being can be stark. By understanding common pests and their seasonal patterns, you can take proactive measures to safeguard your space.
While basic prevention strategies are effective, don’t hesitate to call professionals when infestations escalate. Balancing DIY methods with expert intervention guarantees that your home remains a sanctuary, free from the nuisances of unwanted pests. Stay vigilant, and keep your living environment pest-free.
Essential Tips for Choosing Budget-Friendly CAD Software
November 2, 2024
When it comes to selecting budget-friendly CAD software, you’re likely wondering where to start. You’ve got a design project to tackle, but you don’t want to break the bank. The good news is that you’ve got options - but only if you know what to look for. As you weigh your choices, you’ll need to ponder more than just the price tag. What specific design needs do you need to meet?
What functionality do you require? And what about system compatibility? Answering these questions will help you narrow down your options, but you’ll want to keep exploring to find the perfect fit for your project and your budget.
Determine Your CAD Needs
Your design project’s success hinges on selecting the right CAD software, and that starts with identifying your specific needs. Before searching for cheap CAD software, take a step back and assess your project requirements. What type of design work will you be doing? Do you need 2D or 3D modeling capabilities? Will you be working solo or collaborating with a team?
What’s your budget for software and potential add-ons? Knowing the answers to these questions will help you narrow down your options and find a CAD solution that meets your unique needs. By understanding your requirements, you’ll be able to find a cheap CAD software that’s tailored to your project, rather than settling for a generic, one-size-fits-all solution.
Compare Software Functionality
Several CAD software options claim to offer budget-friendly solutions, but it’s vital to cut through the marketing jargon and compare their functionality to find the best fit for your project. You need to evaluate the features that matter most to you, such as 2D and 3D modeling capabilities, parametric design, and collaboration tools. Make a list of the essential features you require and compare them across different software options.
Consider the level of complexity, user interface, and learning curve of each software. By doing so, you’ll be able to separate the budget-friendly options that truly meet your needs from those that don’t. This will help you make an informed decision and avoid overspending on features you don’t need. Browse around this website to buy cheap CAD software.
Check System Compatibility
Before diving into the world of budget-friendly CAD software, verify the chosen solution is compatible with your computer’s operating system and meets its technical requirements. You don’t want to invest time and money in a CAD software that won’t run smoothly on your machine. Check the software’s system requirements, including the operating system, processor speed, RAM, and storage capacity.
Certify your computer meets these requirements to avoid performance issues. Additionally, check if the CAD software is compatible with your device’s graphics card and display resolution. By doing so, you’ll guarantee a seamless user experience and maximize your productivity.
Evaluate User Support Options
Having verified your computer meets the CAD software’s system requirements, you can now focus on evaluating the user support options provided by the software vendor. Assess the availability of resources, such as online tutorials, user manuals, and FAQs, to guarantee you can quickly resolve any issues that may arise.
Check if the vendor offers email, phone, or live chat support, and what their response times are. Additionally, look for active online communities, forums, or social media groups where users can share knowledge and experiences. Proper user support options can substantially impact your overall CAD software experience, so crucially evaluate them carefully before making a purchase.
Read User Reviews and Ratings
Explore the world of user reviews and ratings to gain invaluable insights from people who have hands-on experience with the CAD software. You’ll get a sense of the software’s strengths and weaknesses, as well as its ease of use, performance, and compatibility. Pay attention to the overall rating and the number of reviews to confirm the feedback is reliable.
Look for reviews from users in your industry or with similar needs to yours. Be cautious of fake reviews and consider multiple sources, such as CAD software review websites, forums, and social media groups. By reading user reviews, you’ll make a more informed decision and avoid potential pitfalls.
Conclusion
You’ve weighed your options and considered the essential factors. Now, make an informed decision that meets your budget and design requirements. Choose a CAD software that aligns with your needs, offers the necessary functionality, and is compatible with your system. Don’t forget to evaluate user support options and read reviews from similar users. By doing so, you’ll find a budget-friendly CAD solution that streamlines your design process and enhances your productivity.
Mastering Adobe Photoshop: Essential Tips for Beginners
October 9, 2024
You're about to access the full potential of Adobe Photoshop. As a beginner, mastering the fundamentals is crucial to start with the basics – understanding the interface and key tools. You're probably already familiar with the concept of editing images, but Photoshop's vast array of features can be overwhelming. You'll want to know how to navigate the Menu Bar, Toolbox, and Options Bar to make the most of this powerful software. But before you can start editing like a pro, you need to know where to start. What are the fundamental tools and techniques you'll need to master first?
Getting Familiar With the Interface
As you plunge into Adobe Photoshop, getting familiar with its interface is crucial to unshackling your full creative potential. The first step is to understand the layout, which remains largely unchanged since Adobe Photoshop 7.0. The interface is divided into several key areas: the Menu Bar, Toolbox, Options Bar, and Document Window. The Menu Bar provides access to various commands and features, while the Toolbox contains a range of tools for editing and manipulating images.
To the top of the screen lies the Options Bar, which displays settings and options for the currently selected tool. Below this lies the Document Window, where your image is displayed. You can resize this window by dragging the edges or using the zoom tool. Adobe Photoshop also allows you to customize the interface to suit your needs. You can resize or reposition the Toolbox and other panels to maximize your workspace.
Essential Tools and Features
Now that you're comfortable exploring Adobe Photoshop's interface, it's time to harness the full potential of its powerful editing tools. Familiarize yourself with the toolbar, where you'll find a range of essential tools for image editing. The Move Tool (V) allows you to reposition objects, while the Marquee Tool (M) enables you to make selections based on shape and size. The Lasso Tool (L) is ideal for selecting complex objects with curved edges.
The Adjustment Layers panel is another essential feature for non-destructive image editing. This panel enables you to apply tonal adjustments, color corrections, and other edits without altering the original image. You can also use the Layer Styles panel to add textures, bevels, and other effects to your layers.
Basic Editing Techniques
With a solid grasp of Photoshop's essential tools, you're ready to plunge into the world of basic editing techniques that will elevate your images to the next level. In photo editing, the key to achieving professional-looking results lies in mastering the fundamentals. One of the most critical techniques is adjusting image brightness and contrast. By using the 'Image' > 'Adjustments' > 'Brightness/Contrast' menu, you can fine-tune your image's exposure to create a more balanced look.
Another essential technique is color correction. The 'Color Balance' tool allows you to adjust the color temperature of your image, removing unwanted casts and achieving a more natural tone. You can also use the 'Hue vs. Saturation' curve to target specific colors and adjust their saturation levels.
Advanced Image Manipulation
You've refined your skills in basic editing techniques, and it's time to push the boundaries of what's possible in Photoshop. Now, it's time to immerse yourself in advanced image manipulation. This is where you can let your creativity shine and take your image edit to the next level.
To start, familiarize yourself with the Select and Mask tool. This powerful feature allows you to make complex selections and refine them with precision. Use the Refine Edge option to fine-tune your selection, and the Radius slider to adjust the edge detection. You can also use the Adjustment Layers to make non-destructive edits to your image.
Conclusion
You've finally mastered the basics of Adobe Photoshop - or so you think. Don't worry, it's a never-ending journey. As you continue to explore the world of photo editing, remember that the more you know, the more you realize how little you know. But that's what makes it exciting. With every new skill, you'll reveal more creative possibilities. So, keep pushing the boundaries and experimenting with new techniques - the real mastery has just begun.
The Role of Online Listings in Discovering Homes for Sale in Phuket
October 5, 2024
Finding your dream home in Phuket can feel like searching for a needle in a haystack. However, online listings have transformed the way we buy property, making it easier to search for homes for sale in Phuket Thailand. This digital shift allows prospective buyers to explore a range of options from the comfort of their couches, or even while sipping a coconut on the beach. Let’s take a closer look at how online listings play a crucial role in this exciting journey.
The Convenience of Digital Searches
In today’s fast-paced world, convenience is key. When you decide to buy a house in Phuket, the first step is often to search online. Websites and platforms featuring listings of Phuket Thailand houses for sale allow you to filter your preferences. Whether you’re looking for a cozy villa by the beach or a modern apartment in the heart of the city, the options are plentiful.
With a few clicks, you can access detailed information about each property. Online listings typically include high-quality photos, virtual tours, and in-depth descriptions. This allows you to visualize your potential new home without stepping foot outside. When you search for homes for sale in Phuket Thailand, you can narrow down your choices based on price, location, and amenities. This level of convenience is hard to beat. Navigate to this website to discover the trusted property company for searching homes for sale in Phuket Thailand.
Access to a Wide Range of Options
One of the most significant advantages of online listings is the sheer variety of properties available. From luxurious villas to quaint cottages, the online marketplace has it all. Searching for a Phuket house for sale means you can explore different neighborhoods and discover hidden gems that you might not have found otherwise.
Real estate agencies like Inter Property Phuket are excellent resources for this. They provide extensive listings of homes for sale in Phuket, ensuring you have access to the latest properties. Their expertise helps you find exactly what you're looking for, whether you want to buy a house in Phuket or rent a house in Phuket Thailand. The vast selection means you’re more likely to find something that feels just right.
Informed Decision-Making
Making a major investment requires careful consideration, and online listings empower buyers to make informed decisions. By having access to various properties and their details, you can compare features and prices easily. This not only helps you stay within your budget but also ensures you’re making a choice that aligns with your lifestyle.
Detailed listings include information on local amenities, schools, and public transportation. This kind of insight is invaluable for families or anyone planning to live in Phuket long-term. When you’re ready to buy a house in Thailand Phuket, having a comprehensive understanding of the area will guide your decision. Moreover, agencies like Inter Property Phuket provide expert advice and market analysis, further enhancing your ability to make a well-rounded choice.
The Importance of Working with a Top-Rated Agency
While online listings are a fantastic resource, partnering with a reputable real estate agency can take your home search to the next level. Agencies like Inter Property Phuket specialize in helping you search for homes for sale in Phuket Thailand and guide you through the process of buying a house in Phuket. Their experience and local knowledge are invaluable assets.
A good agency will not only help you find a Phuket house for sale but also assist those looking to sell their house in Phuket Thailand. They provide insights on pricing, marketing, and property management, ensuring your investment is in good hands. With their support, navigating the real estate market becomes a breeze.
In conclusion, online listings have revolutionized the way we search for homes for sale in Phuket. They offer convenience, variety, and essential information that empower buyers to make informed decisions. Whether you’re ready to buy a house in Phuket or simply exploring options, leveraging these digital tools, along with the expertise of Inter Property Phuket, can make all the difference. Embrace the journey of finding your dream home in this tropical paradise, and enjoy every moment of the adventure.
How to Maintain and Extend the Life of Your Custom LED Light Strips?
September 27, 2024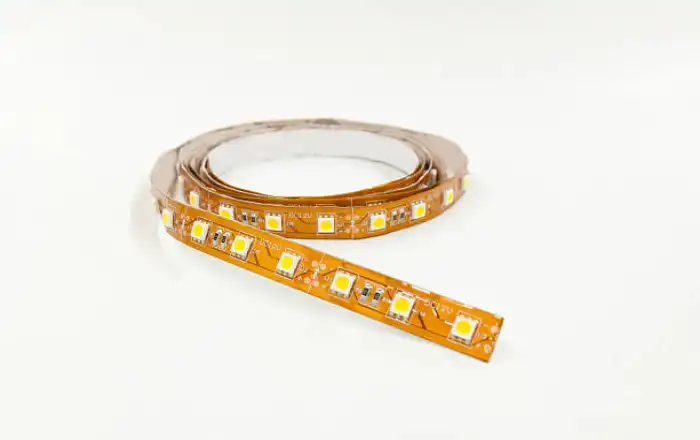
If you've invested in custom LED light strips, you're likely looking for ways to maximize your investment. With proper care, these strips can provide years of reliable service, but neglect can cut their lifespan short. To start, understanding the importance of regular cleaning and how it impacts your LED light strips' performance is crucial. But cleaning is just the beginning - there are several other key factors to ponder. By taking the right steps, you can notably extend the life of your custom LED light strips, but what are those steps, and how do you implement them?
Cleaning Your LED Light Strips
Cleaning your LED light strips regularly is essential to keeping them functioning at peak levels. Dust, dirt, and other contaminants can accumulate on the surface of the LED strip light, reducing its brightness and overall efficiency. When cleaning your LED tape light or LED ribbon light, it's vital to avoid using harsh chemicals or abrasive materials that can damage the LED strip's protective coating.
Instead, use a soft, dry cloth to gently wipe away any debris or dust from the surface of the LED strip. For more stubborn stains or dirt buildup, you can dampen a cloth with distilled water and gently clean the area. Be careful not to get any liquids into the LED strip's electrical components. It's also essential to follow the manufacturer's cleaning instructions, as some custom LED neon strips or bespoken neon flex strip may have specific cleaning requirements.
Handling Power and Temperature
Cleaning your LED light strips regularly is only part of maintaining their peak performance. To further extend their lifespan, you must handle power and temperature correctly. When using a ULEDsupply LED strip light, verify that you follow the manufacturer's guidelines for maximum power input. Overpowering your LED strip can cause it to overheat, leading to premature degradation. When it comes to temperature, it's vital to keep your LED strip within the specified operating range. CCT COB LED strip manufacturers, such as CCT COB LED strip manufacturers, typically specify a maximum operating temperature. Exceeding this temperature can cause a significant reduction in the strip's lifespan.
To manage temperature, consider using a heat sink or thermal adhesive to dissipate heat away from the LED strip. You can also use a dimmer or pulse-width modulation (PWM) to reduce the strip's power consumption. When purchasing from a reputable LED strip supplier, such as a custom neon flex strip manufacturer or custom LED neon strip manufacturer, confirm that they provide detailed specifications and recommendations for temperature management.
Installation and Mounting Tips
When it comes to installing and mounting your LED light strips, guaranteeing a secure and even application is crucial for peak performance. To achieve this, you'll need to choose the right type of LED strip for your project. For instance, if you're working with a custom CCT COB LED strip, consider the specific requirements for heat dissipation and adhesive properties. ULED Supply LED strip lighting often comes with a variety of adhesive options, so select the one that best suits your installation needs.
When mounting the LED strip, make sure the surface is clean, dry, and free of dust or oils. For superior results, use a high-quality adhesive or clips specifically designed for LED strip lighting. If you're working with a custom LED neon strip supplier, verify that the material is compatible with the LED strip's requirements. Additionally, avoid applying excessive pressure or stress on the LED strip, as this can damage the delicate components.
Storage and Replacement Practices
Proper storage and handling of LED light strips are essential for maintaining their performance and extending their lifespan. When storing your ULEDsupply LED light strip, guarantee it is protected from physical damage and environmental factors such as moisture, dust, and extreme temperatures. Avoid folding or creasing the LED tape light, as this can cause damage to the circuit board or LEDs. Instead, roll the strip up gently and secure it with tape to prevent tangling.
When replacing a damaged section of your CCT COB led strip, carefully disconnect the power source and remove any mounting clips or adhesives. Identify the faulty section and cut the strip at the nearest cut line using a sharp utility knife or wire cutters. Dispose of the damaged section and replace it with a new one from a reputable wholesale CCT COB led strip supplier, such as a custom neon flex manufacturer.
Conclusion
By following these maintenance tips, you'll be the master of your custom LED light strips' destiny, guiding them through a long and radiant life. A gentle touch, a watchful eye on power and temperature, and careful handling will be the keys to tapping into their full potential. With these best practices, your LED light strips will shine brighter for years to come, a beacon of efficiency and effectiveness in your creative endeavors.
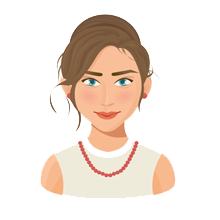
Contact Me
803 2nd Street, Suite F.
Davis, CA 95616
t: (973) 605-6062
f: (956) 263-2766